NEMA 6 उच्च अचूकता असलेले दोन-फेज 4-वायर 14 मिमी हायब्रिड स्टेपर मोटर
वर्णन
ही NEMA6 मोटर एक हायब्रिड स्टेपर मोटर आहे ज्याचा व्यास तुलनेने लहान आहे १४ मिमी.
ही मोटर उच्च अचूकता, लहान आकाराची हायब्रिड स्टेपर मोटर आहे जी सुंदर दिसते आणि उत्कृष्ट कामगिरी देते. ही स्टेपर मोटर बंद लूप एन्कोडर/फीडबॅक सिस्टमशिवाय देखील अचूकपणे नियंत्रित आणि प्रोग्राम केली जाऊ शकते.
NEMA 6 स्टेपर मोटरचा स्टेप अँगल फक्त 1.8° आहे, म्हणजेच एक आवर्तन पूर्ण करण्यासाठी त्याला 200 पावले लागतात.
सभोवतालचे तापमान -२०℃~५०℃ आहे.
आयुष्यमान ६००० तासांपेक्षा जास्त आहे.
जर तुम्हाला मोटरबद्दल काही प्रश्न असतील तर अधिक व्यावसायिक समर्थनासाठी कृपया आमच्याशी संपर्क साधा.
पॅरामीटर्स
स्टेप अँगल | १.८°±५% |
टप्प्यांची संख्या | २ टप्पा |
रेटेड व्होल्टेज | ६.६ व्ही |
वर्तमान/टप्पा (A/टप्पा) | ०.३अ(पीक व्हॅल्यू) |
टॉर्क धरून ठेवणे | किमान ०.०५८ किलो-सेमी |
फेज रेझिस्टन्स | २२Ω±१०%(२०℃) |
फेज इंडक्टन्स | ४.२ मिलीएच±२०%(१ हर्ट्झ १ व्ही आरएमएस) |
डायलेक्ट्रिक शक्ती | एसी ५०० व्ही/५ एमए कमाल |
रोटर इंनेर्टिया | ५.८ ग्रॅम-सेमी² |
वजन | ०.०३ किलो |
इन्सुलेशन वर्ग | ब (१३०°) तापमान वाढ ८० के कमाल |
डिझाइन रेखाचित्र
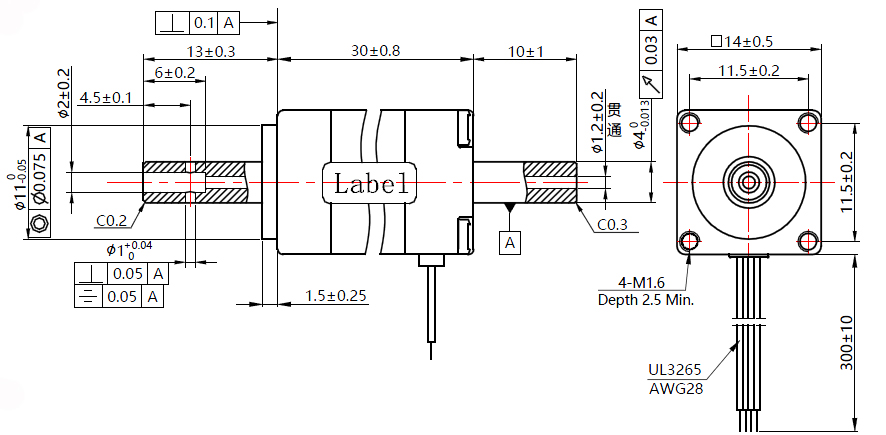
NEMA स्टेपर मोटर्सची मूलभूत रचना
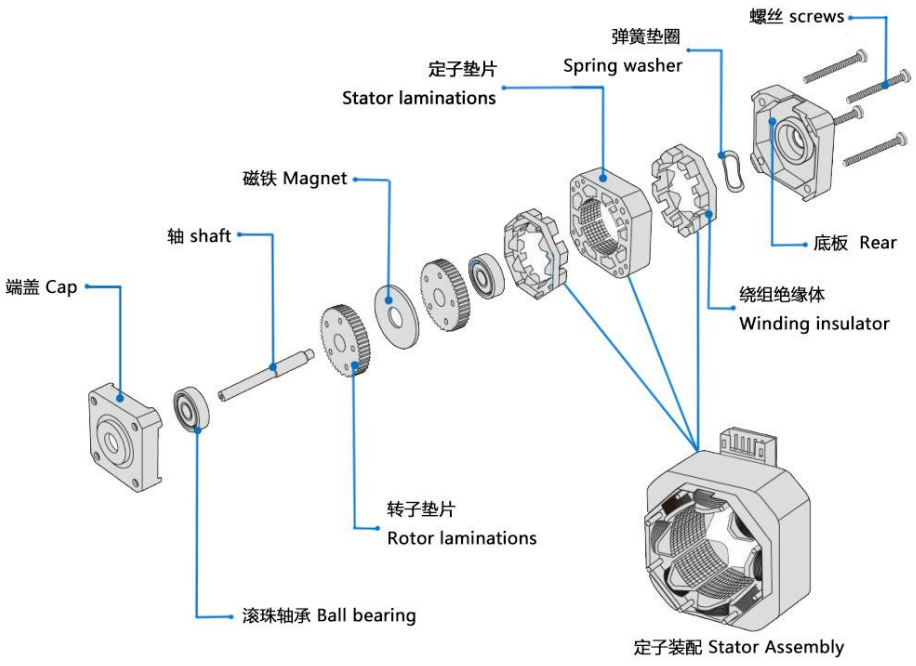
हायब्रिड स्टेपर मोटरचा वापर
हायब्रिड स्टेपर मोटर्सच्या उच्च रिझोल्यूशनमुळे (प्रति क्रांती २०० किंवा ४०० पावले), ते उच्च अचूकता आवश्यक असलेल्या अनुप्रयोगांसाठी मोठ्या प्रमाणावर वापरले जातात, जसे की:
३डी प्रिंटिंग
औद्योगिक नियंत्रण (सीएनसी, स्वयंचलित मिलिंग मशीन, कापड यंत्रसामग्री)
संगणक उपकरणे
पॅकिंग मशीन
आणि इतर स्वयंचलित प्रणाली ज्यांना उच्च अचूकता नियंत्रण आवश्यक आहे.
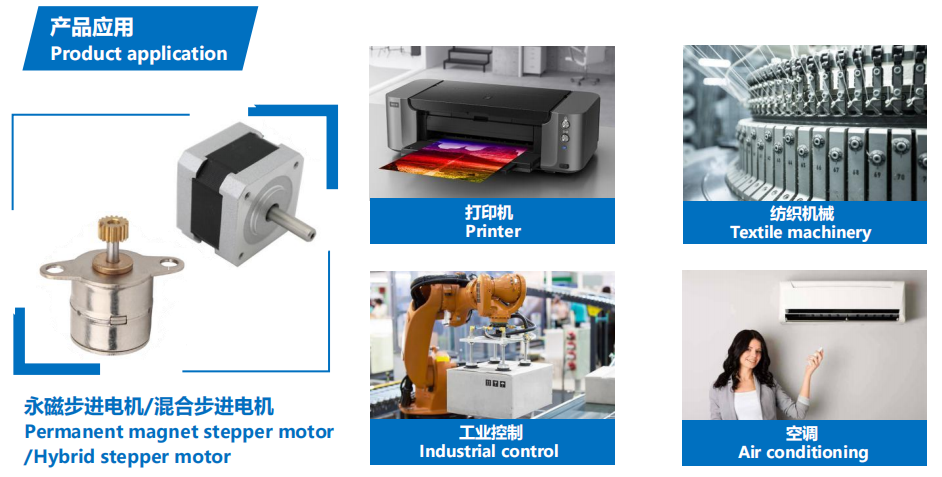
हायब्रिड स्टेपर मोटर्सबद्दल अनुप्रयोग नोट्स
ग्राहकांनी "प्रथम स्टेपर मोटर्स निवडणे, नंतर विद्यमान स्टेपर मोटरवर आधारित ड्रायव्हर निवडणे" या तत्त्वाचे पालन करावे.
हायब्रिड स्टेपिंग मोटर चालवण्यासाठी फुल-स्टेप ड्रायव्हिंग मोड न वापरणे चांगले आणि फुल-स्टेप ड्रायव्हिंगमध्ये कंपन जास्त असते.
हायब्रिड स्टेपर मोटर कमी-वेगाच्या प्रसंगांसाठी अधिक योग्य आहे. आम्ही सुचवितो की वेग १००० आरपीएम (०.९ अंशांवर ६६६६पीपीएस) पेक्षा जास्त नसावा, शक्यतो १०००-३०००पीपीएस (०.९ अंश) दरम्यान असावा, आणि त्याचा वेग कमी करण्यासाठी तो गिअरबॉक्सने जोडता येतो. मोटरमध्ये उच्च कार्यक्षमता आणि योग्य वारंवारतेवर कमी आवाज आहे.
ऐतिहासिक कारणांमुळे, फक्त नाममात्र १२ व्ही व्होल्टेज असलेली मोटर १२ व्ही वापरते. डिझाइन ड्रॉइंगवरील इतर रेटेड व्होल्टेज मोटरसाठी सर्वात योग्य ड्रायव्हिंग व्होल्टेज नाही. ग्राहकांनी स्वतःच्या गरजेनुसार योग्य ड्रायव्हिंग व्होल्टेज आणि योग्य ड्रायव्हर निवडावे.
जेव्हा मोटर जास्त वेगाने किंवा मोठ्या भाराने वापरली जाते तेव्हा ती सामान्यतः थेट कामाच्या वेगाने सुरू होत नाही. आम्ही हळूहळू वारंवारता आणि वेग वाढवण्याचा सल्ला देतो. दोन कारणांसाठी: पहिले, मोटर पावले गमावत नाही आणि दुसरे, ते आवाज कमी करू शकते आणि स्थिती अचूकता सुधारू शकते.
मोटर कंपन क्षेत्रात (६०० पीपीएसपेक्षा कमी) काम करू नये. जर ती मंद गतीने वापरायची असेल, तर व्होल्टेज, करंट बदलून किंवा काही डॅम्पिंग जोडून कंपनाची समस्या कमी करता येते.
जेव्हा मोटर ६०० पीपीएस (०.९ अंश) पेक्षा कमी तापमानात काम करते, तेव्हा ती कमी प्रवाह, जास्त प्रेरक शक्ती आणि कमी व्होल्टेजने चालविली पाहिजे.
मोठ्या प्रमाणात जडत्व असलेल्या भारांसाठी, मोठ्या आकाराची मोटर निवडावी.
जेव्हा जास्त अचूकता आवश्यक असते, तेव्हा गिअरबॉक्स जोडून, मोटरचा वेग वाढवून किंवा सबडिव्हिजन ड्रायव्हिंग वापरून ते सोडवता येते. तसेच ५-फेज मोटर (युनिपोलर मोटर) वापरली जाऊ शकते, परंतु संपूर्ण सिस्टमची किंमत तुलनेने महाग आहे, म्हणून ती क्वचितच वापरली जाते.
स्टेपर मोटर आकार:
आमच्याकडे सध्या २० मिमी (NEMA8), २८ मिमी (NEMA11), ३५ मिमी (NEMA14), ४२ मिमी (NEMA17), ५७ मिमी (NEMA23), ८६ मिमी (NEMA34) हायब्रिड स्टेपर मोटर्स आहेत. हायब्रिड स्टेपर मोटर निवडताना आम्ही प्रथम मोटरचा आकार निश्चित करण्याचा आणि नंतर इतर पॅरामीटरची पुष्टी करण्याचा सल्ला देतो.
कस्टमायझेशन सेवा
ग्राहकांच्या गरजेनुसार मोटरची रचना समायोजित केली जाऊ शकते ज्यामध्ये हे समाविष्ट आहे:
मोटरचा व्यास: आमच्याकडे ६ मिमी, ८ मिमी, १० मिमी, १५ मिमी आणि २० मिमी व्यासाची मोटर आहे.
कॉइल रेझिस्टन्स/रेटेड व्होल्टेज: कॉइल रेझिस्टन्स अॅडजस्टेबल असतो आणि जास्त रेझिस्टन्ससह, मोटरचा रेटेड व्होल्टेज जास्त असतो.
ब्रॅकेट डिझाइन/लीड स्क्रू लांबी: जर ग्राहकांना ब्रॅकेट लांब/लहान हवा असेल, माउंटिंग होल सारख्या विशेष डिझाइनसह, ते अॅडजस्टेबल आहे.
पीसीबी + केबल्स + कनेक्टर: पीसीबीची रचना, केबलची लांबी आणि कनेक्टर पिच हे सर्व समायोज्य आहेत, ग्राहकांना गरज भासल्यास ते एफपीसीमध्ये बदलता येतात.
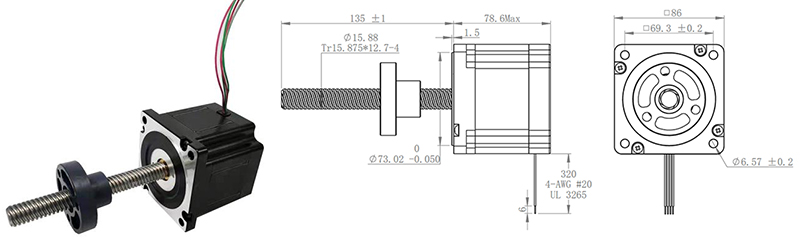
आघाडी वेळ
जर आमच्याकडे नमुने स्टॉकमध्ये असतील तर आम्ही ३ दिवसांत नमुने पाठवू शकतो.
जर आमच्याकडे नमुने स्टॉकमध्ये नसतील, तर आम्हाला ते तयार करावे लागतील, उत्पादन वेळ सुमारे २० कॅलेंडर दिवस आहे.
मोठ्या प्रमाणात उत्पादनासाठी, लीड टाइम ऑर्डरच्या प्रमाणात अवलंबून असतो.
पेमेंट पद्धत आणि पेमेंट अटी
नमुन्यांसाठी, सर्वसाधारणपणे आम्ही पेपल किंवा अलिबाबा स्वीकारतो.
मोठ्या प्रमाणात उत्पादनासाठी, आम्ही T/T पेमेंट स्वीकारतो.
नमुन्यांसाठी, आम्ही उत्पादनापूर्वी पूर्ण पेमेंट गोळा करतो.
मोठ्या प्रमाणात उत्पादनासाठी, आम्ही उत्पादनापूर्वी ५०% प्री-पेमेंट स्वीकारू शकतो आणि उर्वरित ५०% पेमेंट शिपमेंटपूर्वी गोळा करू शकतो.
आम्ही ६ पेक्षा जास्त वेळा सहकार्य करून ऑर्डर दिल्यानंतर, आम्ही इतर पेमेंट अटी जसे की A/S (दृश्यानंतर) वाटाघाटी करू शकतो.
वारंवार विचारले जाणारे प्रश्न
१. नमुन्यांसाठी सामान्य वितरण वेळ किती आहे? बॅक-एंड मोठ्या ऑर्डरसाठी वितरण वेळ किती आहे?
नमुना ऑर्डर लीड-टाइम सुमारे १५ दिवस आहे, मोठ्या प्रमाणात ऑर्डर लीड-टाइम २५-३० दिवस आहे.
२. तुम्ही कस्टम सेवा स्वीकारता का?
आम्ही मोटर पॅरामीटर, लीड वायर प्रकार, आउट शाफ्ट इत्यादींसह उत्पादने सानुकूलित स्वीकारतो.
३. या मोटरमध्ये एन्कोडर जोडणे शक्य आहे का?
या प्रकारच्या मोटरसाठी, आपण मोटर वेअर कॅपवर एन्कोडर जोडू शकतो.